Electric Vehicle
Assembly Line
CASE STUDY
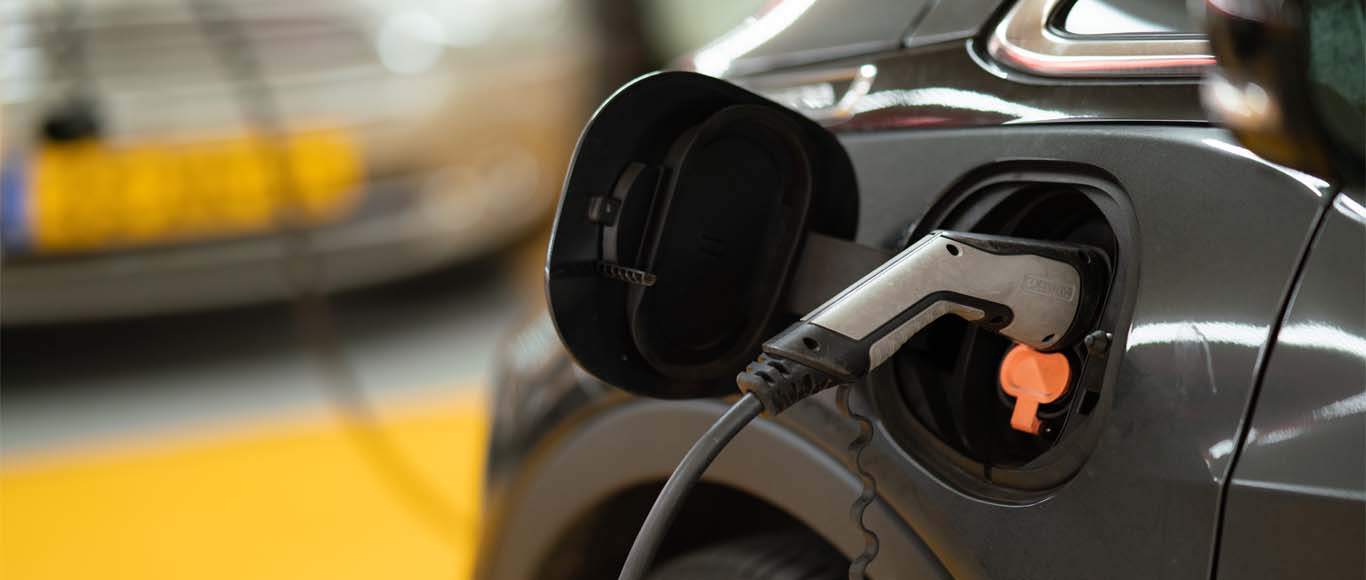
THE SITUATION
Electric vehicles (EVs) are on the rise. Most car companies have entered the race to get their share of the EV market. General Motors has their future laid out in front of them, starting with the success of their Chevy Bolt. This car with a 259 mile range started off as the cheaper alternative to more luxurious EVs from other American automakers. As of now, the race is fully on to produce an inexpensive EV for the masses.
It all starts in production. GM needed a solution to getting the Bolt’s battery packs into the vehicles, which are being suspended on a rail system. These batteries are heavy, weighing in at around 1,000 lbs. – although that is just a fraction of our Hydraulic Lift Table’s capacities of up to 8,000 lbs.
The Solution
See the Hydraulic Lifts in Action
The Result
By implementing the hydraulic lift tables, GM is able to efficiently position their battery packs under the chassis of the Chevy Bolt, making it ergonomic for technicians and engineers to assemble and work on the vehicle.