Ways to control AGVs
AGV Navigation
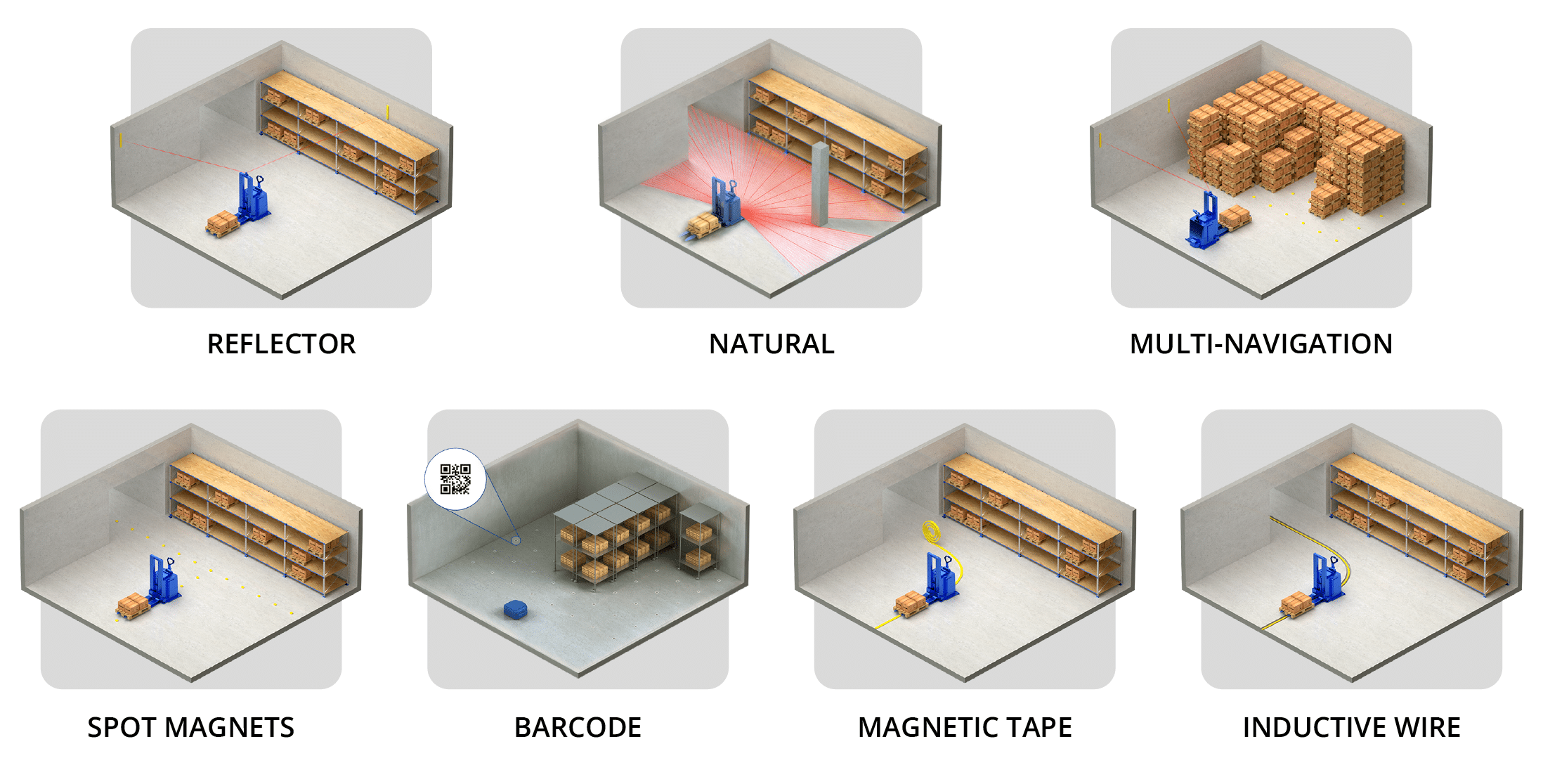
Not sure which navigation option you need?
Request a free consultation
Question & Answer
What is the difference between AGV and AMR? Why AGV?
AGVs (Automated Guided Vehicles) are guided by a preset path and will stick to that path. When an object is detected, the AGV will come to a stop until the object is removed from the path.
AMRs (Autonomous Mobile Robots) operate independently and can move around obstacles freely. However, most manufacturing applications use AGVs since assembly lines feature little to no variables or obstacle appearances.