Super-Conducting
Magnet Manufacturing
CASE STUDY
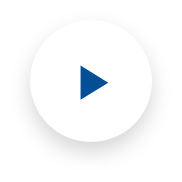
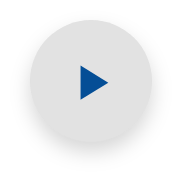
THE SITUATION
General Atomics needed to move their superconducing magnets around their manufacturing space. The facility is equipped with a 35-ton crane; however, each magnet and its support structure weigh in excess of 200 tons. Further complicating matters, the highly sensitive magnets must be kept level within .01 inch to avoid putting undue stress on it.
THE SOLUTION
Custom Built
The company partnered with Airfloat to create a custom transporter for magnet transport at ground level.
How it Works
The large u-shaped machine uses air casters to gently float up to 400,000 lbs. in any lateral direction. Built-in lifting jacks raise and lower the magnets several feet.
How it's Controlled
The machine is steered via a wireless controller and is capable of maneuvering in circles, around corners and other complex movement patterns.
The Result
General Atomics uses the Airfloat transporter to quickly and easily move each magnet from workstation to workstation, where it is wound with 3.5 miles of superconducting cables, insulated, heat-treated and the like. When the magnets are complete they will be shipped to Southern France, where they will form the backbone of a $20-billion fusion reactor slated to power up in 2020.
WANT TO READ MORE ABOUT AIRFLOAT AND MANUFACTURING?
DOWNLOAD THE FULL CASE STUDY