Large Vehicle Manufacturing with AGV Technology
How an AGV System Streamlines Production
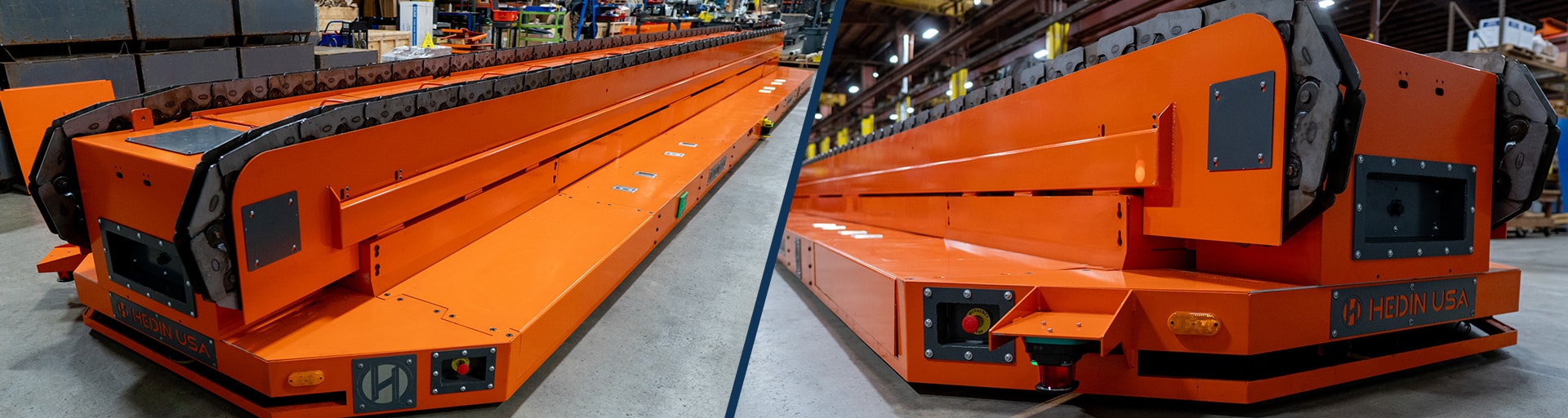
Key Points
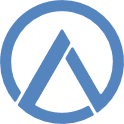
33% Production Growth
The implementation of automation has enabled the client to increase their production by 33%, going from 60 to 80 vehicles a day.
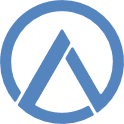
40ft Battery Transporter
Designed and built to the client's specifications, the battery-powered transporter was constructed to handle 10,000 lbs. and efficiently moves it throughout the plant.
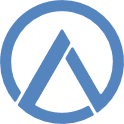
Savings with Automation
The automation partner of the heavy industry is here; our Flatbed Transporter is fitted with hardware to safely and automatically drive along the assembly process.
-Blake Ringger, Machine Design Engineer
Conclusion
The integration of AGVs into the vehicle manufacturing process significantly enhanced operational efficiency, flexibility, and safety. This case study demonstrates the potential of automation in manufacturing, showing how tailored technological solutions can address complex logistical challenges and contribute to achieving production goals.